Design of a cotter joint
- Abhi Shejul
- Jun 11, 2021
- 5 min read
Updated: Jul 2, 2021
Every product is designed to sustain failures. But how do we know the point of failure of that structure?
Table of contents
4.1 Failure in rod
7. Summary
8. Short video
Earlier we had seen about the cotter joint and how is the assembly made. We understood the functionality of the components involved in the assemble along with the significance of the joint. If you have not read it yet, please check our previous blog and join us again.

To design a component, we need to take a number of factors into consideration. The design not just involves the dimensioning of the components but also the choice of material and structural balance to loading conditions. For any structural element or assembly, there is a loading criterion. This loading criterion is depending on the area of application and tenure as well. While designing any element, it is essential to consider the factor of safety. What is the factor of safety though?
Factor-of-safety is the configuration value for a design or product to define the strength of the product. It is the ratio between the actual capacity of the element to the demand value.

The factor of safety value should always be greater than one. This means that the element should be designed to withstand a higher load than what it is actually is going to bear. For example, to design a park bench for 3 people, consider the design to withstand weight if 9 people. The factor-of-safety for the bench is 3.
Factor of safety is important while building any structure. It defines that the product is capable of
tolerating extra load than it is intended to carry. This is beneficial in cases where the structure might get overloaded and doesn't succumb to the situation.
Understanding the factor-of-safety with the failures in a cotter joint.
The application of cotter joint involves the assembly having to undergo lateral loading forces. A typical cotter joint will experience tensile or compressive forces along the axis. As we have studied earlier, lateral forces in one direction causes shearing forces in the perpendicular plane. As a result, a cotter joint will experience shearing forces as well.
σ = F / A
where,
σ is the stress applied, F is the force applied, A is the area of the force application.
Now that we know the loading conditions, we need to see the maximum requirement. The maximum requirement will be the demand value. Hence, when we will be configuring the design to withstand loads higher than the demand value. How much higher? It depends on the factor of safety we use.
Before we jump into what are the different design specifications for the components of the cotter joint, let us take a look at how the forces are acting on the elements. Tensile forces cause tensile stress on the element and this stress value is used to calculate the dimensional elements of the assembly. Similarly, the shear stresses are used for calculating the dimensions of assembly.
Each component of the assembly has its specific configuration for the design. Let's assume an assembly for cotter joint as below:

Let us consider the parameters in the assembly as below:

The different components of a cotter joint are as follows:
Rod
A rod is the tailing end of the spigot and cotter. It has a cylindrical cross-section hence the only dimensional parameter is diameter ‘d’. The rod experiences tensile load and induces tensile stress. The maximum permissible load for the rod in tension is as below:
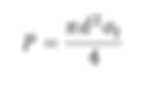
Spigot
A spigot is the end of the rod which is inserted into the socket cavity. The cavity is of rectangular geometry. This rectangular cavity causes shearing in the spigot end. The maximum permissible load for the various conditions is as below:
Failure condition: Tensile stress in the connecting rod.
The area which experiences this tensile stress is the cross-section area of the rod minus the thickness area of the cotter slot.



Failure condition: Crushing of spigot end
The region in spigot experiences crushing due to the force induced in the contact region with the cotter. The area is along the rectangular slot and causes crushing failure.

Failure condition: Crushing of spigot collar
The collar is useful for aligning the spigot into the socket cavity such that the cotter can be wedged into the rectangular slot in the spigot and socket. The collar is rested against socket collar and experiences resistance as the assembly experiences tension force. The spigot collar has ring like cross section area, which will undergo crushing upon failure.

Failure condition: Shearing of spigot end
The section of the spigot, from the rod end to the slot experiences shearing. The contact between the cotter and spigot transmits the load onto the section.
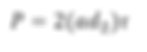
Failure condition: Shearing of spigot collar
The segment of the spigot is collar just like the previous case, but the area in question is different one. The collar ring will experience resistance, which induces shearing in the central region of the spigot collar.

Socket
A socket has different profiles, collar and rod with slot for cotter. A collar is helpful in alignment of the spigot in the cotter. This exposes collar to a resistance force. Thus, spigot collar experiences tension as well as crushing force.
Socket end has rectangular slots to allow the cotter to pass through. This slot cavity experiences shearing which can cause failure. The maximum permissible load for different failure conditions are:
Failure condition: Tension across the slot of socket
The area under tension is the section of the socket at the cotter slot region. The tension through the connecting rod is passed into the section. Area of the weakest section of socket resisting tensile failure.

Failure condition: Crushing of socket collar
The socket collar and the cotter wedged through the rectangular slots interact at this section of socket. The vertical cotter region in contact resists the tension force in the socket/rod which could cause crushing of the socket collar in the socket-cotter interaction region.

Failure condition: Shearing of socket end
In this case, the conditions are similar to there previous one but it's along the length of the socket collar (c). But, as opposed to tension the section experiences shear stress.

Cotter
Cotter is the key component of the cotter joint assembly. Cotter is wedged in the slot between spigot and socket. The tension force in the spigot and socket ends causes shearing of the cotter. Hence, the cotter experiences shearing force. The maximum permissible load for a cotter to resist failure is as below.
Failure condition: Shearing in cotter

So far we have looked at the forces in the different elements of the cotter assembly. How does the factor of safety bud in? Let's take a look.
If the FoS is 1.8, and the it is expected to withstand 100N, then the force considered while designing the component is 180N.

This value of force is used in the above equations as permissible stress/load value. Along with the load value, we can calculate the dimensions of the components. Hence, if we know the maximum permissible stress value of the material and the load requirements, we need to substitute those values in the equations and get the dimensional parameters configured accordingly.
Summary:

Cotter Joint has mainly three components – spigot, socket, and cotter.
When the cotter is inserted into the slot, the central portion of the cotter comes in contact with the spigot and the spigot gets pushed into the socket till the collar of the spigot comes in contact with the collar of the socket.
The factor of safety is the design safety parameter which allows the structure to have a strength greater than the required strength.
A cotter joint is subjected to tensile load and corresponding tensile stresses are developed in the assembly.
Different components of the cotter joint experience either compressive or crushing stresses.
These stresses can induce failure of the joint. Hence, maximum permissible force is used to configure the design of the joint.
Short Video:
The maximum permissible load equations we looked at are for a cotter joint only. Do you know about other failure conditions in a cotter joint? Different design elements will have different permissible loads. What are these different design elements? Please subscribe to Mech n Flow to know more about such content!